Efficient logistics in the beverage and food industry
News General news
Securing transport without loss of time and damage: Automated palletising system with optimised stretch-wrapping technology reduces film use by up to 55 per cent. Software enables different pallet formats and remote maintenance via R-Connect.
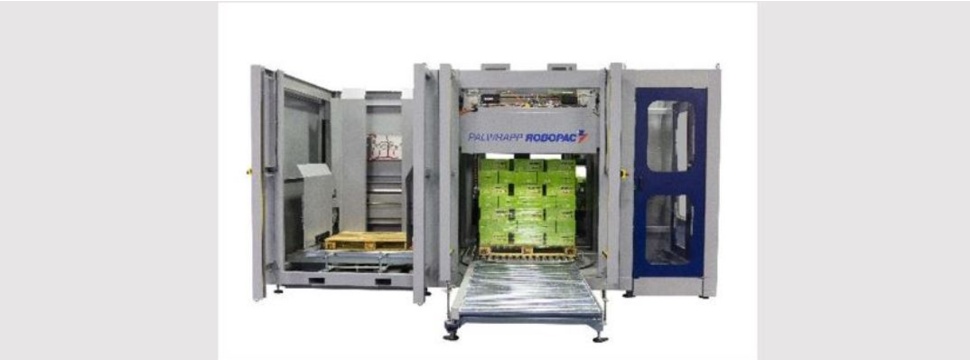
Millions of companies face the same challenge every day: goods such as food and beverages must be carefully palletised and wrapped. Only high precision in this process can ensure that the pallets remain stable throughout the entire transport route and are then stored safely. In addition, the stretch film should be correctly dimensioned: If it is wrapped incorrectly, the goods can fall off the pallet or be damaged by film that is wrapped too tightly. The cost of the film material should also not be underestimated. The Palwrapp from Robopac provides a remedy: the optional semi-automatic or fully automatic system arranges products up to 2.7 m high on the most common pallet formats and then wraps them. It uses the proven Cube technology, which ensures maximum load stability during stretch wrapping while using the film sparingly. With its compact dimensions, the Palwrapp can even be used in locations with little available space, such as in small and very small businesses.
The use of pallets has revolutionised world trade and logistics: According to the European Pallet Association e.V., around 450 to 500 million standardised Euro pallets alone are in circulation worldwide to standardise the transport of goods. "When it comes to the correct arrangement of cartons or cans, just a few millimetres decide on the stability of the entire pallet and thus whether the goods arrive undamaged at their destination," explains Kerstin Conzelmann, Marketing Manager at Robopac Germany. "To avoid high costs, for example if the products are damaged, companies must therefore proceed with special care." However, several problems arise in the process: For one thing, the logistics industry is increasingly under time pressure, so that individual process steps such as palletising have to be carried out almost every minute. On the other hand, there are globally established standard formats such as (half) Euro or CHEP pallets. But how and at what height the food or beverages are layered is determined individually for each pallet - there is no "patent recipe" that applies equally to all goods.
"Companies then have two options: Either workers take over palletising by hand, or they acquire a palletising machine that carries out this process independently and in a calculated manner," Conzelmann says. "However, while manual palletising is highly error-prone and also involves a high risk of accidents for employees, palletising robots are usually inflexible and can only be adjusted to different goods and pallet sizes to a limited extent. A lot of time is therefore lost with both approaches." Space requirements also play an important role, because fully and semi-automatic palletising systems usually take up a relatively large amount of space and can only be integrated into logistics at great expense. The reason for this is the expensive warehousing, which is why space must be used as efficiently as possible and there is little room left for larger systems.
Cube technology enables film savings of up to 55 per cent
Flexibility, as little space as possible and easy operation - these are the requirements that a palletising solution should fulfil. The Palwrapp from Robopac meets these requirements. The palletiser, which can operate either semi-automatically or fully automatically, first sorts the goods to be stacked, such as cartons or crates, which are fed to the system on a conveyor, according to a specific pattern. This distributes the goods stably on the pallet. The exact arrangement and number of layers can be defined in the Palwrapp's software. Furthermore, up to 350 kg can be stacked per layer.
After all goods have been palletised, the fully automatic wrapping takes place. "The Palwrapp is equipped with the proven Cube technology," reports Conzelmann. "This ensures that the amount of film and the force with which the film is wrapped around the goods are precisely matched to the pallet. So for more sensitive goods such as fruit and vegetable boxes, the Palwrapp applies less force than for less sensitive goods such as canned goods." Even for each individual layer stacked on the pallet, the amount of force can be adjusted individually. In this way, the technology used ensures, on the one hand, a particularly high level of stability so that the goods cannot suddenly topple over during transport. On the other hand, it prevents the goods from being damaged by a film that is wrapped too tightly. The Palwrapp also reduces the amount of material required, because the particularly efficient wrapping technology can save between 30 and 55 per cent of the film and thus significantly reduce material costs.
Compact design enables operation even in narrow logistics halls
The Palwrapp also offers advantages over other palletising solutions when it comes to space requirements: the system requires an area of 7,416 x 5,155 mm in the fully automatic version and 4,095 x 2,535 mm in the semi-automatic version - which means that an area of less than 10m2 is needed. The maximum height depends on the module chosen, with two different versions available at 1,750 and 1,400 mm respectively. Commissioning is also particularly easy thanks to the plug-and-play principle. The Palwrapp also has a 10.1-inch touchscreen display. Via the Human Machine Interface (HMI) and the integrated software, various settings can be made, such as the arrangement of the goods or the number of layers. It is also easy to create new positioning patterns, for example, to efficiently palletise and stretch-wrap half Euro pallets or pallets with dimensions of 1,200 x 1,200 mm. The software was especially designed for user-friendliness and intuitive operation; the machine can be operated by workers without programming knowledge. This makes the Palwrapp particularly flexible, so that a wide variety of palletising tasks can be handled without any loss of time.
All moving parts are equipped with servo motors so that the system operates almost wear-free and guarantees a long service life. At the same time, energy consumption is at a particularly low level. Thanks to the user-friendly operator interface, the operation of the machine can also be monitored. The HMI is equipped with three safety levels to protect personnel from injury. In addition, malfunctions and alarms can be displayed and statistics can be called up via the display. Robopac Germany also offers remote maintenance in case of queries or problems, which is carried out via the proven R-Connect system. This makes it possible to reduce downtime to a minimum and a technician does not have to come by to carry out repairs or maintenance work. "The Palwrapp thus combines all of Robopac's technologies to simplify pallet handling," explains Conzelmann. "In this way, companies save time and money while using less energy and materials, and ensure the safe transport of their goods."