Prevent expensive and image-damaging recall campaigns: Acoustic sensors reliably detect glass breakage within production and filling lines
News General news
Connection to SPS allows automatic sorting out of damaged products
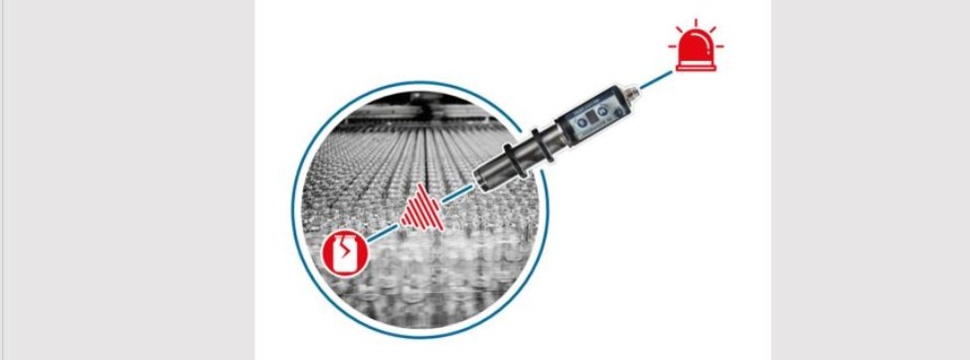
Wherever food or beverages are filled into glass containers such as bottles or jars, they may burst. The resulting splinters sometimes contaminate other units in the immediate vicinity. If the glass breakage is not detected immediately, the affected products can end up on the market and, in the worst case, all the way to the end customer. At the latest then, elaborate and cost-intensive recalls of entire batches are necessary, which not only annoy the customer base, but also cause lasting damage to the manufacturer's reputation. To prevent this problem from arising in the first place, Schwerin-based ds automation gmbh has developed special acoustic sensors. These can be easily integrated into existing lines and reliably detect glass breakage incidents by signal level and frequency characteristics. Depending on the degree of automation, the line is then either stopped for manual inspection or the affected units are automatically ejected from the filling line. The sound sensors used here are dustproof and watertight in accordance with protection class IP67 and made entirely of stainless steel, so that they also meet the high hygiene requirements in food and beverage production.
"In the portal produktwarnung.eu, there were already twelve entries with the keyword 'glass splinter' or 'glass breakage' in the DACH region in the first seven months of 2022," reports Dipl.-Ing. Christian Schröder, developer at ds automation gmbh. "For the manufacturers concerned, this not only means an enormous cost, but also the trust that their buyers and end customers place in them is permanently damaged." In addition, the entire batch has to be recalled, which means that perfect products are also inevitably disposed of. In the worst case, if the recall does not reach individual consumers in time, their health is at risk.
"Such incidents and their far-reaching effects occur in the first place because there is no uniform standard solution for glass breakage detection in food and beverage bottling lines," Schröder knows. Some companies use optical detection systems, which, however, are based on relatively complex and cost-intensive measurement technology. Others rely only on time-consuming and labour-intensive manual inspection. With its dsound® airborne sound sensors, on the other hand, ds automation has designed an efficient method for the reliable detection of glass breakage that has been established for around ten years, specifically for the needs of the food and beverage industry.
Reliable and cost-effective quality assurance via airborne sound
"The sensors for glass breakage detection are special microphones that continuously monitor their environment," Schröder explains. "They detect any deviation from a sound situation defined as normal." For this purpose, specific trigger thresholds are defined in advance, within which the usual background noise of the production line ranges. The noise generated by a glass breakage can be characterised as a bang, which is very broadband and has a relatively high signal amplitude. This exceeds the set threshold and can accordingly be identified as an anomaly by the sensor.
However, a major challenge in detecting glass breakage events with the help of airborne sound is the sound attenuation by the air itself and the interference noise of the production line. However, the closer the sensors are placed to the sound event to be measured, the lower the air attenuation and thus also the susceptibility to errors. "In most production lines, there are certain points where the units usually burst - for example, during the separation processes or the filling process," Schröder explains. A rupture can occur there, for example, if individual bottles or jars are pre-damaged, misaligned or the filling quantities are not set correctly. "We make use of this knowledge by installing the sound sensors close to the concrete 'problem spots' and eliminating interfering factors," Schröder continues.
Furthermore, the risk of false alarms increases with the usually relatively loud ambient noise of the production lines, because of which employees often have to wear hearing protection. The measurement technology specialists at ds automation get around this problem by not only measuring the sound level, but also performing band-pass filtering. In this way, for example, the measurement signal can be concentrated on the frequency spectrum between 16 kHz and 32 kHz, which is barely or not perceptible to the human ear. In this way, the sound event triggered by breaking glass can be reliably identified and appropriate follow-up steps can be initiated.
Flexible parameterisation for different applications
"In order to avoid both false alarms and undetected incidents, we always configure the sensors individually to the needs of the application," says Schröder. "For example, a bursting beer bottle that is preloaded under pressure produces a rather muffled bang, while a bursting jar of food produces a high-frequency sound event." In addition, it can be useful to increase the precision of the measurement by limiting it to the specific time period of an expected breaking moment, for example when a gripper grasps a unit. Depending on the degree of automation of the filling line, the sound sensor can be connected to the respective line control or a higher-level PLC for this purpose. If the integrated signal analysis and evaluation of the sensor identifies a breakage event, then the line is stopped in accordance with the internal production processes, for example, to enable a manual check. In highly automated systems, the sensor can also cause the affected units to be ejected without delay and, depending on the product type and industry, to be fed into cleaning or necessary destruction processes, for example.
The respective settings can be made on the factory-preconfigured sensor with the help of a display and two buttons. For logging or data export, it can also be connected to a PC via standard interfaces. The sound sensor itself is certified to protection class IP67 and is made entirely of easy-to-clean stainless steel, so that it also meets the high hygiene requirements in the food and beverage industry and withstands aggressive cleaning agents. In combination with a magnetic excitation unit, dsound® sound sensors can also be used to check glass containers with metal closures such as crown caps for leaks. Due to the non-contact measurement technology via airborne sound, the sensor is maintenance-free and can be easily installed on new or existing production lines. "Our customers from different application areas have already been successfully using the airborne sound sensors for ten years and more for line monitoring and quality assurance of their products," Schröder confirms in conclusion.