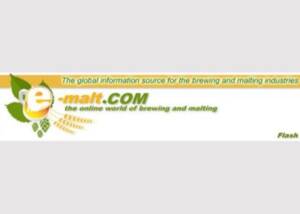
News for the beverage industry
Do you want to learn more? Here you will find news about beverages and the beverage industry, they are also sorted by different categories - General news from the beverage industry, jobs, trade fairs, offers and requests. Would you also like to appear with your press releases here? Just contact us.
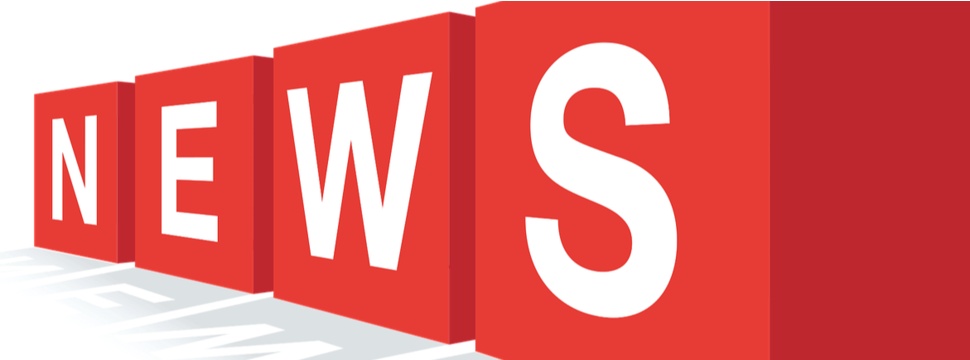
This page shows you the latest news from all beverage-world.com news categories.
You want to see general news regarding the beverage industry?
Find the appropriate category and read the interesting news. Here companies are looking for employees or employees are searching for a new job, companies report about innovations or their new sales manager. Other companies inform about their participation in trade fairs or about surpluses from production that can be sold at favorable prices.
Are you looking for a new employee? You have developed a new and innovative beverage packaging? You participate in a trade fair and exhibit your new products there?
If you answered "yes" to at least one of these questions, then you have come to the right place.
Would you also like to publish your news here? Get in touch with us. Just use our contact form.
Birkner hopes you enjoy reading these news.