Digitalising production processes
News General news
SCHÄFER Container Systems is optimising quality assurance and investing in a digital x-ray machine
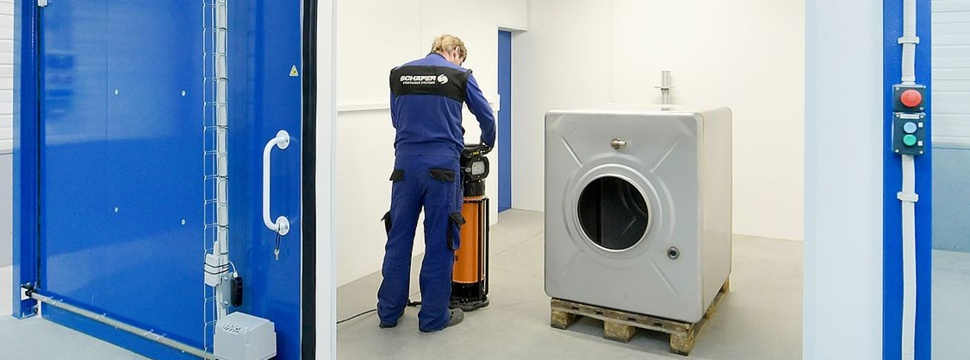
With the stationary ISOVOLT Titan series X-ray machinefrom General Electric, SCHÄFER Container Systems, manufacturer of beverage containersystems, IBCs and customized containers, is making a significant addition to its qualityassurance facilities. Switching from analogue to digital for the non-destructive testing ofweld (NDT) enables more stringent quality control and is a further step in the transitiontowards a digital factory.
Shorter exposure times, the complete elimination of developer chemicals, a higher degree ofautomation and the significantly improved image quality persuaded SCHÄFER ContainerSystems to make the investment-intensive switch to the latest digital X-ray technology internallyfor NDT. SCHÄFER Container Systems will use this non-destructive test procedure to detectand make visible any unwanted contaminants, pores, cavities, cracks, incomplete welds anddeviations in weld seam shape and dimensions in stainless steel IBCs and KEGs.
The new state-of-the-art X-ray machine has been installed at SCHÄFER Container Systems in aspecially equipped shielded room to provide the required radiation protection. In the X-raychamber, workpieces with external dimensions of up to 3,000 mm x 4,000 mm x 2,500 mm(width x depth x height) can undergo radiographic examination. To ensure the digital X-raysystem is operated safely, SCHÄFER Container Systems had an employee trained as an X-rayspecialist.
The main beneficiaries of this are all those customers whose individual quality and testingrequirements are implemented, monitored and digitally logged seamlessly on site in theproduction plant. The efficiency gain can be quantitatively measured in terms of significantlyreduced reaction times in production operations. Thanks to this digital imaging process, fullyautomatic image evaluation for defined fault characteristics is now possible – a notablemilestone in the digitalisation of production processes.